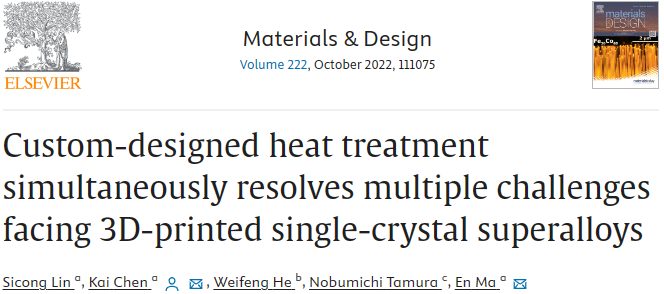
Single-crystal Ni-based superalloys are currently the material of choice for turbine blade applications, especially with the emerging additive manufacturing (AM) that facilitates the manufacture/repair of these single crystals. This promising AM route, however, comes with a dilemma: in the fusion and heat affected zones after e-beam or laser induced melting, one needs a solutionizing annealing to relieve the residual stresses and homogenize the chemical/microstructure. The super-solvus solutionizing temperature is usually adopted from the protocol for the cast superalloys, which almost always causes recrystallization and stray grain growth, resulting in a polycrystalline microstructure and degrading the high-temperature mechanical performance. Here we demonstrate a custom-designed post-printing heat treatment to replace the conventional super-solvus one. The recovery and relatively low temperature diminish the driving force for recrystallization and the movement of stray grain boundaries, without suffocating the chemical/microstructural homogenization thanks to the narrow dendrite width and short element segregation distance. The optimal duration of the heat treatment is proposed to achieve atomic-diffusion mediated chemical homogenization while limiting γ′-particle coarsening in the interdendritic regions. Our strategy makes it practically feasible to resolve several bottleneck problems with one processing/treatment, removing a seemingly formidable obstacle to effective additive manufacturing of superalloy single crystal products.
Link:https://doi.org/10.1016/j.matdes.2022.111075